Have you ever wondered where your clothing comes from? Or how your wardrobe goes from raw materials to that soft cotton T-shirt or gauzy viscose maxi dress?
Assembling clothing requires a huge workforce: from the farmer that harvests hemp or cotton, to the warehouse worker who delivers the finished product to the retailer.
There is plenty of opportunity for something to go wrong along the way, and when it does, those costs pass along to the consumer in the retail price. Post-Covid supply chain woes have made us more aware than usual of the interconnectedness of the production process and the multitude of problems that stem from how things are done. They’ve also led to many businesses exploring how to do things better at each step.
By examining three of the biggest challenges faced by garment manufacturers currently, we not only understand how these problems impact what we pay for the latest styles, but also the responsibility these companies have to address the concerns of workers as well as consumers.
Rising Costs
The fashion industry has not escaped inflation. Beyond the increased cost of procuring raw materials, the increase in gas prices means that every aspect of the garment’s manufacturing – from farm to fabric creation to garment manufacturer to retailer – is seeing a nudge. Also, a weak dollar itself impacts significant relationships with farms and factories in China and elsewhere. The lower the value, the more money it takes to move materials through the supply chain to the consumer.
Man-Made Disruptions
COVID. The War in Ukraine. Human rights issues and labor disputes. Regulations and tariffs. Some of these events, while related to the people who make our clothing, are beyond the direct control of retailers and manufacturers. More concerning are the issues directly caused by the actions (or in some cases inaction) of these businesses.
According to Business of Fashion, labor rights have steadily declined since before Covid, in 11 regions that are key to the fashion industry including China, India, Mexico, Pakistan, and Vietnam. Poor working conditions and wage violations create a high turnover rate in the garment manufacturing industry. Brands that push factories to lower costs often find these cuts passed on in the form of labor abuses and health and safety violations.
US politicians have recently introduced a Bill to encourage reshoring among producers and ensure that American garment workers are protected. The FABRIC Act, which stands for Fashioning Accountability and Building Real Institutional Change, would help to revitalize the garment industry in the United States by improving working conditions, preventing wage theft, and investing in domestic clothing production. A separate piece of legislation, The Fashion Act, is being pursued by leaders in the state of New York and asks companies to be responsible for their impact in supply chains, through a legally binding Mandatory Due Diligence Framework.
Sustainability and Environmental Issues
For something to be considered sustainable, it must be produced in a way that is ethical – meaning both environmentally friendly and safe for the people who make the product as well as for the consumer.
In the US, there are very few regulations concerning the chemicals used to make our clothing. Currently, the US only bans 11 hazardous chemicals. In comparison, neighboring Canada has banned 457.
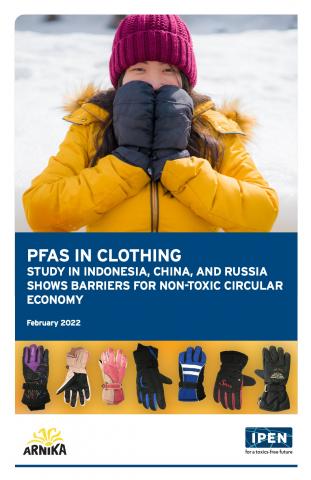
One of several scientific studies that explore potential “forever chemicals” in clothing.
Recently, companies that have billed products as environmentally sustainable, like Thinx and REI, have faced lawsuits for false advertising. Garments produced by these companies have been found to contain high levels of perfluoroalkyl and polyfluoroalkyl substances, or PFAS, which are linked to cancer, thyroid dysfunction, small changes in birth weight, and high cholesterol. PFAS cause pollution at every stage of production. PFAS chemical manufacturing facilities and garment factories often contaminate the air, water, and soil of the surrounding environment, as well as impacting the people who work in these places.
Only companies doing business in California are required by law to state if a product may contain hazardous chemicals. In the meantime, experts warn that if you purchase clothing that is advertised as “waterproof,” “stain resistant,” or “dirt repellant,” you should assume that PFAS have been used in the production. The US has set out to regulate older-generation versions of these chemicals, which they view as more harmful and long-lasting “forever chemicals,” but stricter state-level bans in large markets like California, Washington State, and New York, present a fresh challenge to manufacturers.
Key Solutions for Companies and Consumers
Brands and designers have been tasked with finding viable solutions for these multifaceted problems. In an article for Forbes, author and fashion industry expert Alison Bringe cautions that brands must create long-lasting change or face continued scrutiny and the possible loss of loyalty from consumers who are becoming increasingly globally conscious.
To address these three broad supply chain issues, a manufacturer’s response should include the following elements:
Transparency. According to the Human Rights Watch, a transparent manufacturing supply chain “better enables a company to collaborate with civil society in identifying, assessing, and avoiding actual or potentially adverse human rights impacts.” Not only is this good for the workers – it reduces the uncertainty that many consumers face when purchasing products, not sure if the garment is sustainably produced by workers who are paid fairly in a safe working environment.
Diversification and Redundancy: Sourcing raw materials from a wide array of suppliers not only reduces the chances of supply disruption, but it can strengthen the company’s bargaining power, helping to lower prices for the customer. Furthermore, sourcing closer to the end market can also help to mitigate some transportation struggles and reduce the overall environmental impact of importation.
Vertical Integration: Typically, manufacturers are the central component of a supply chain, meaning that they purchase raw goods from one seller and hire another to transform them into a finished product, which they market to consumers through brand labels and sell to retail stores. Manufacturers achieve vertical integration when they control or own elements beyond their typical reach, by buying companies or establishing contracts with other businesses to provide goods and services that are part of the manufacturing and distribution process at fixed rates. This level of influence makes the company more adaptable to consumer demand, among other things.
As a shopper, If your end goal is to keep your wardrobe budget low while purchasing from ethical, sustainable manufacturers, your best course of action is two-fold: avoid fleeting fashion trends and invest in timeless core pieces made by companies with transparent manufacturing practices. While some mainstream companies may provide a viable alternative, made-to-measure is a great alternative to the normal retail rut. Though up front costs may seem a bit higher, there are several key benefits:
- Custom-made garments are a great value. Because they are made from quality materials, custom clothing from Balodana designers are meant to last for more than a single season. While it may appear convenient to purchase a new favorite dress every few months, over time it may cost you more, especially if you factor in your time.
- Made-to-measure is sustainable and more transparent. Because they are not governed by a faceless corporate entity, bespoke designers are able to curate relationships with those who create their garments as well as the suppliers they use to source raw goods. Moreover, the small number of garments produced means there’s less waste during the creation process. Furthermore, creators like Merces use only natural and sustainably produced fabrics, including locally sourced linen and hemp. Other companies like Shantima use fabric scraps to create coordinating accessories.
- Custom clothing is made for your body. This means you spend less time searching for sales, shopping the racks, getting frustrated in fitting rooms, or returning purchases made online or in the store. Our step-by-step measurement process is simple and something you can do at home or with a friend. Also, you only have to do it once and you’re ready to order for a formal occasion, business meeting, or your next vacation!
Resources
- The Fashion Act S.7428 (Biaggi) / A.8352 (Kelles) https://www.thefashionact.org/
- The FABRIC Act / S.4312) (Gillibrand / Maloney) https://thefabricact.org/
- https://www.fashionfwd.org/uspolicies
- https://www.wgrz.com/article/money/economy/supply-chain-expert-explains-united-states-cotton-shortage/71-ccd49a3e-0fa5-4812-b5d7-2d1409c707c5
- https://www.just-style.com/features/how-to-tackle-the-apparel-supply-chains-biggest-problems/
- https://www.voguebusiness.com/companies/bottlenecks-at-the-ports-labour-disputes-and-congestion-threaten-us-fashion-supply-chain
- https://www.fibre2fashion.com/industry-article/3202/inflation-grips-the-apparel-supply-chain
- https://www.bqprime.com/business/summer-wardrobe-makeover-will-pinch-even-as-cotton-prices-ease
- https://www.voguebusiness.com/companies/bottlenecks-at-the-ports-labour-disputes-and-congestion-threaten-us-fashion-supply-chain
- https://cosmosmagazine.com/people/garment-supply-chain-slavery/
- https://www.forbes.com/sites/forbescommunicationscouncil/2023/01/02/the-state-of-sustainability-in-the-fashion-industry-and-what-it-means-for-brands/?sh=710afa6b1c82
- https://www.scmr.com/article/union_strikes_labor_deal_with_west_coast_ports